Three Costly Mistakes Manufacturing Companies Make With Their IT
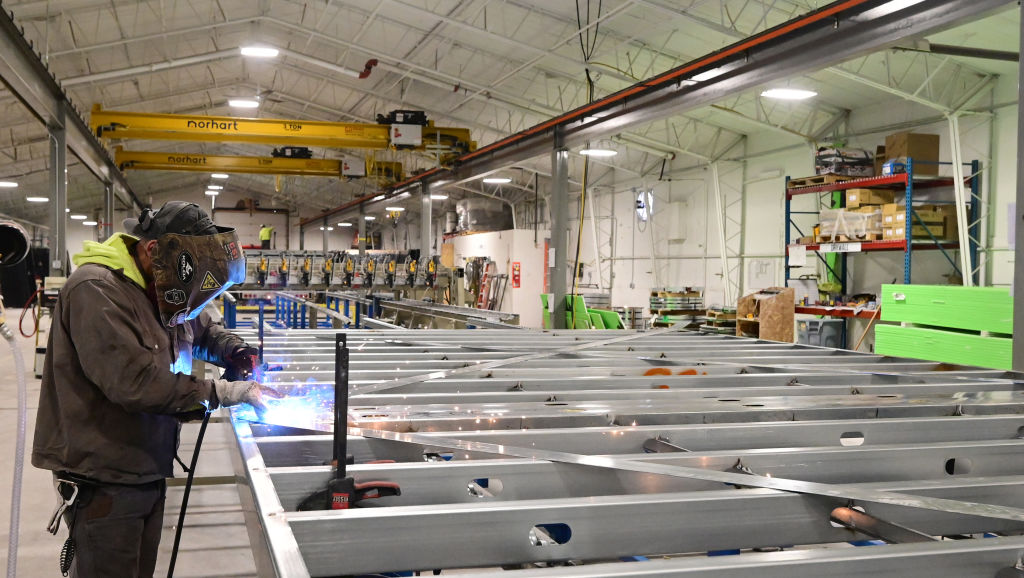
I stepped onto the production floor of a precision parts manufacturer in Marietta last month and immediately noticed something odd. The shop floor was buzzing with activity—CNC machines humming, automated material handlers moving smoothly between stations—yet in the corner, an operator was manually entering production data into a clipboard.
Why not input that directly into your system?” I asked.
The floor manager laughed. “Our production software crashes whenever we try to input data in real-time. IT says it’s a ‘known issue’ they’ll fix eventually. We’ve been hearing that for eight months now.”
This disconnect isn’t unusual. Through my consulting work with manufacturing operations across Georgia, I’ve witnessed firsthand how specialized technology needs often conflict with traditional IT support approaches. The results can be frustrating at best and financially devastating at worst.
Let’s examine three of the most expensive mistakes I regularly encounter—and the approaches that forward-thinking manufacturers are using to solve them.
Mistake #1 – Treating Production Technology Like Office IT
The most pervasive mistake occurs when companies apply standard office IT support models to manufacturing environments. These environments have fundamentally different requirements:
Downtime Calculations That Miss the True Cost
When an office worker’s computer crashes, the cost is relatively straightforward—lost productivity for that employee until service is restored. In manufacturing, the calculation becomes exponentially more complex:
- Direct labor costs for idle production workers
- Lost contribution margin from unproduced goods
- Potential material waste from interrupted processes
- Expediting costs to meet customer commitments
- Quality issues from rushed production recovery
A metal fabricator in Douglasville recently calculated that a single hour of downtime on their production line costs $8,700—over 20 times what they had previously estimated when considering only direct labor costs.
Response Time Expectations That Don’t Match Reality
Standard IT service level agreements (SLAs) commonly promise 4-hour response times for critical issues and next-business-day for standard problems. In manufacturing, these timeframes can be catastrophic.
“Our previous IT provider considered ‘critical’ to mean total system failure,” explained the operations director at a food processing facility in Lawrenceville. “But for us, a 20% slowdown in our inventory scanning system could mean missing a shipping deadline to a major retailer—potentially a six-figure problem. They just didn’t understand our operational priorities.”
Specialized IT support for manufacturing companies addresses these unique requirements through:
- Custom SLAs aligned with production schedules and true business impact
- On-site spare parts for critical systems to enable immediate repairs
- Remote monitoring systems that detect performance degradation before failure
- Cross-trained technicians who understand both IT and operational technology
- Documented recovery procedures specific to each production system
Mistake #2 – Neglecting the IT/OT Integration Gap
The second costly mistake occurs at the intersection of traditional information technology (IT) and operational technology (OT). Historically separate, these systems are now increasingly interconnected—creating both opportunities and challenges.
The Knowledge Gap Challenge
Most traditional IT professionals lack experience with industrial control systems, programmable logic controllers (PLCs), SCADA systems, and other manufacturing-specific technologies. Conversely, manufacturing engineers typically understand production equipment but not enterprise networking or cybersecurity.
This knowledge gap creates serious vulnerabilities:
- Security configurations that either compromise production or leave systems exposed
- Integration points that fail during critical operations
- Data exchange problems between business systems and shop floor equipment
- Inadequate disaster recovery planning for production systems
A plastic injection molding company in Suwanee discovered this gap during a system upgrade when their IT provider accidentally reconfigured their network in a way that prevented their molding machines from communicating with their production scheduling system. The result? Three days of manual production coordination and dozens of missed deadlines.
Building the Integration Bridge
Leading manufacturers address this integration challenge by working with specialized IT support for manufacturing companies that bring expertise spanning both domains:
- Teams with backgrounds in both manufacturing and information technology
- Experience with industrial protocols like Modbus, Profinet, and OPC-UA
- Understanding of real-time data requirements for production systems
- Knowledge of manufacturing-specific applications and their integration points
“The turning point for us came when we found a provider whose technicians had actually worked in manufacturing environments,” noted the IT director at a aerospace parts manufacturer in Kennesaw. “They immediately understood our concerns about implementing security patches during production runs and helped us develop a staged approach that protected our systems without disrupting operations.”
Mistake #3 – Implementing Generic Cybersecurity in Production Environments
The third critical mistake involves applying office-oriented cybersecurity approaches to manufacturing environments without considering their unique operational requirements.
The Security vs. Availability Conflict
Manufacturing systems prioritize availability above all else—equipment must run when needed to meet production schedules. This fundamental requirement often conflicts with standard security practices:
- Regular patching schedules that require system reboots
- Aggressive endpoint protection that can interfere with real-time controls
- Multi-factor authentication that complicates operator access during shifts
- Network segmentation that disrupts necessary communication between systems
“An IT consultant once locked down our production network following ‘best practices’ from their office clients,” recalled the CIO of a chemical processing facility in Conyers. “Our production literally stopped because the PLCs couldn’t communicate with their supervisory systems. It took three days to unravel the mess.”
Manufacturing-Specific Security Approaches
Effective IT support for manufacturing companies implements security differently:
- Tailored patch management that aligns with production maintenance windows
- Security controls tested for compatibility with industrial protocols
- Passive monitoring systems that detect anomalies without disrupting operations
- Identity management designed for shift workers in high-pressure environments
- Network segmentation that protects critical systems while enabling necessary communication
A food processing facility in Gainesville worked with specialized manufacturing IT experts to implement a security model that achieved compliance requirements without compromising production reliability. Their approach included a separate industrial DMZ (demilitarized zone) for production systems, application-level gateways for necessary data exchange, and scheduled security maintenance aligned with their production calendar.
Finding Manufacturing-Focused IT Support
For manufacturing operations seeking to avoid these costly mistakes, finding the right IT support partner represents a critical business decision. Based on my experience with dozens of Georgia manufacturers, several criteria separate truly effective manufacturing IT partners from those merely claiming the capability:
Vertical Experience Matters Most
Look for providers who can demonstrate:
- Specific experience supporting your type of manufacturing environment
- Understanding of industrial control systems and production equipment
- Familiarity with manufacturing applications like MES, ERP, and PLM
- Knowledge of regulatory requirements specific to your industry
Ask potential providers what percentage of their client base consists of manufacturers similar to your operation.
Operational Understanding, Not Just Technical Skills
The most effective partners demonstrate clear understanding of manufacturing operations:
- They discuss technology in terms of production impact, not just technical specifications
- They understand concepts like OEE (Overall Equipment Effectiveness) and lean manufacturing
- They recognize the true cost of downtime in production environments
- They align maintenance with production schedules rather than conventional IT windows
Specialized OT Security Capabilities
Given the unique security challenges in manufacturing, specialized capabilities are essential:
- Experience securing industrial control systems without compromising reliability
- Understanding of manufacturing network architecture and segmentation
- Knowledge of industry-specific frameworks like IEC 62443
- Ability to balance cybersecurity with operational requirements
Conclusion
As manufacturing technology continues to evolve, the gap between traditional IT support and specialized manufacturing